Sometimes it is easy for a productive company such as FAIST to state they work for this or that industry. It is not necessarily so easy, though, to have a vertical integration and technologies that allow serving the customers in their best interests. FAIST Industrial Business Unit is doing just that, since its team has started working with customers active in the Utilities and Smart Metering business. From strategically sourcing the raw materials, to delivering the assembled product with the required level of quality, the team covers it all. Let’s give voice to the people who work on this kind of projects day in and day out, to see what it really entails.
Razvan Tiponut (Project Manager in the Industrial Customer Team)
How long have you been working as Project Manager for the Utilities and Smart Metering part of FAIST’s Industrial BU?
My first role with this account was to support the industrialization of the smart gas meter projects from an engineering standpoint: I have been working as an Application Engineer for 6 months, collaborating with my colleagues in the Customer Team. After this period, I started to cover Project Management responsibilities; therefore, it is about 4 years now.
Since when is FAIST active in Utilities & Metering?
We started to deliver the first products at the beginning of 2016 for a specific European market, after a few years of R&D, project tweaks and co-engineering with the client. Being this a business that is closely linked to the certification of utilities and installation companies, and to governmental approvals, starting a new project can be quite a slow process.
Has the introduction of this new business field been long?
The implementation of the project up to serial volumes extended for a long period, starting with the definition of the customer requirements. The next step was to develop and build specific assembly and welding lines, die tools, and in parallel, to purchase the equipment needed for the whole flow and start the training of our team. At the time being, also for products we consider high-runners, we still continue to implement and adapt our processes as new or different requirements arise. FAIST Metalworking, our manufacturing site in Oradea (Romania), currently delivers caseworks to the customer, where they cover the EMS (electronic manufacturing services) processes themselves.
This part of the project was crucial for FAIST as a supplier, considering that the EMS mentioned previously (the final assembly) was done in different places of the world (in Europe and Asia) - hence we have been forced to consider this, building a casework suitable to be used for all of the customers’ plants, wherever their location.
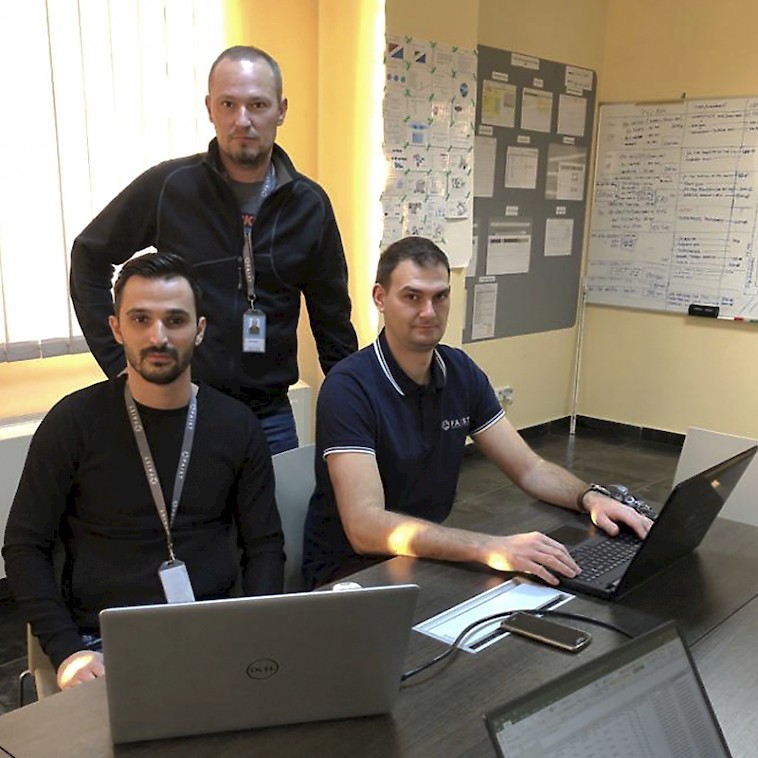
From left to right: Razvan Tiponut (Project Manager in the Industrial Customer Team), Marius Mois (Customer Quality Department) and Adrian Vidican (Manufacturing, Assembly Department).
Please describe the different technologies, productive processes and flows (also intercompany) related to the UMT business at FAIST.
The metal forming is one of the most important processes applied by FAIST for the production of the meters. Subject to the type of components (dimensions, complexity, and so on), these are stamped on different press machines (different tonnage and capabilities) in various FAIST manufacturing locations.
Another key component of the casework are two cylindrical bosses, which are needed to connect the gas meter itself to the gas pipes. These are produced by FAIST Componenti using fully automated CNC milling machines.
The manufacturing site located in Oradea is the one from where the gas meters are delivered around the world. Here the stamping of the main components is done with high tonnage press machines where transfer system lines are fitted to ensure a high-speed process. This is followed by a painting process done internally on an automatic painting line and a welding process carried out on two different carousel lines.
As final step, the assembly process is done using three assembly lines built to support the volumes for all of the different models and projects. Here the parts are labeled for traceability proposes and the bosses are assembled together with the case applying a chemical with the aim to ensure a better sealing. After the final step, the parts are stored inside of an automated vertical warehouse to allow the curing of the sealant.
What are the most crucial steps of the production of a smart gas meter?
Of course, being the product used to deliver and measure gas flow in households, the most important thing is to avoid leaks and to ensure that all of the components produced and assembled in our lines are properly handled from a quality standpoint. Not least, a good visual appearance is another aspect that has to be met.
Lorenzo Selleri (Manufacturing, Machining Department)
What have been the changes in FAIST Componenti’s Machining department implemented due to the start of the UMT business?
The introduction of the UMT business at FAIST has made the machining department grow from a technological and procedural point of view. We purchased two DMG multi-spindles milling machines, which allow us to maintain high productivity thanks to the presence of six spindles working simultaneously. Each of these two machines has a robotic piece-unloading island. The functions performed by these robotic islands are first piece blowing to remove shavings, then length control and later packing on crates.
Major improvements have been made to speed up tool changes with the aim of reducing downtime and improving efficiency. Other activities are still ongoing to ensure continuous improvement. Industry 4.0 is an example of this: it will soon allow us to pour automatic parts and monitor the status of the machine remotely.
Adrian Vidican (Manufacturing, Assembly Department)
How does the assembly process of a smart gas meter differ from the assembly of any other system produced by FAIST?
The assembly processes we perform at FAIST can be classified as removable assembly (with screws) and non-removable assembly, done by riveting, pressing and welding.
For the UMT business we work on three assembly lines, all of which are versionable and can manufacture three types of smart gas meters caseworks. These lines have been designed and built to allow the assembly of the two main components of the smart gas meters caseworks: the inner and outer case.
The assembly process is performed using five assembly workstations for each line, a vertical storage warehouse for each assembly lines, one leak testing workstation and one last final labeling workstation.
A minimal description of the process: the layout design used in each line is cellular, because it has been proven to be the most efficient for this type of product, composed from two parts (Inner case and Outer case) that need to be put together.
Each workstation is designed to fulfill the one-piece flow concept requirements in order to ensure timing between workstations, quality and high productivity efficiency. All of the workstation are equipped with Poka-Yoke systems to avoid any possible mistake during the assembly.
After the assembly process, the parts are stored for 24 hours in the vertical storage warehouse. We are using this kind of storage because the capacity of one line is 1000 parts per shift, and if we were to keep them on the shop floor, the space needed would be huge. The vertical storage warehouse is used for the curing of the special sealants applied.
After 24 hours, the parts are taken out of the vertical storage warehouse. The casework is then ready to be tested for any leaks with a custom leak test machine. The leak test machine is very accurate because is using Helium, a very light gas, as a leak test component.
The final step of the process is realized at the final labeling workstation where the two components (Outer case and inner case) are checked for any esthetic flaw according to a defined procedure, registered as a final product, packed and ready to be delivered.
Marius Mois (Customer Quality Engineering)
What have been the actions taken specifically for UMT to ensure the quality of the product delivered to the customer?
As a general way of operating in FAIST Group, since the development phase of the process, we start with the PFMEA analysis based on the client DFMEA and drawing requirements. For all critical points identified in PFMEA, in the conception of the equipment and assembly lines, our goal is to be covered with Poka-yoke systems, mainly in occurrence if the process allows us. This is a process of continuous improvement, updated according to problems encountered throughout the life of the product.
During the assembly process, an SPC tool, implemented for CTQ dimensions, provides a quality improvement framework for monitoring process health.
What role do safety concerns play in this matter?
Working on a gas meter, safety is obviously our first concern, as all products must leave assembly line leak free. For this reason, products are checked and certified at 100% with a specific Helium test that is able to identify any leakage issue related to assembly process or raw materials used to build the Gas Meter.
Full traceability is also an important matter. Data with all test result and process parameters are registered and stored for every single product, in our internal database.